Bezpieczeństwo maszyn
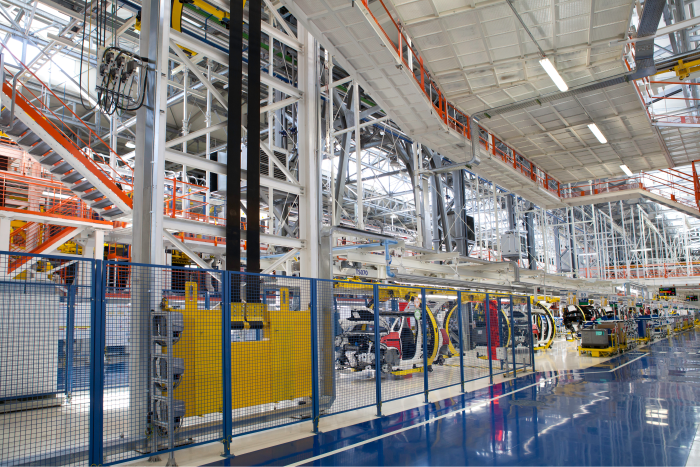
W dobie coraz większej automatyzacji produkcji, coraz szybszych linii technologicznych i robotów przemysłowych jednym z głównych zmartwień nowoczesnego przemysłu jest bezpieczeństwo funkcjonalne.
Chęć zapewnienia komfortu pracy, przy zachowaniu efektywności działania systemów automatyki stawia przed inżynierami coraz większe wyzwania. Mnogość sprzętu chroniącego operatorów przed niepożądanym działaniem maszyny może przyprawiać o ból głowy, a idąc dalej trudność w odnalezieniu się w świecie, gdzie „żółte” komponenty są wszędzie. Rozwiązanie jest proste – inteligentna integracja.
Trochę teorii
Bezpieczeństwo funkcjonalne to wg definicji norm PN-EN 61508 i PN-EN 61511: przyrządowy system bezpieczeństwa (Safety Instrumented Systems – SIS). Jest to zazwyczaj część systemu automatyki maszyny, za pomocą której redukuje się ryzyko do poziomu tolerowanego. Oczywiście przed projektantami systemów bezpieczeństwa stoi trudniejsze zadanie, bo już sama konstrukcja i sposób działania maszyny oraz wszystkie jej peryferia powinny zapewniać bezpieczeństwo użytkowania. Poprzez odpowiednie zastosowanie komponentów bezpieczeństwa dąży się do osiągnięcia zamierzonego poziomu bezpieczeństwa (określanego poprzez Safety Integrity Level lub Performance Level).
Określenie wymaganego poziomu PL wg EN ISO 13849-1
Trudne zadanie
Niektóre zadania wymagają kompletnego układu automatyki i robotyki przy zachowaniu bezpieczeństwa na najwyższym poziomie. Takim przykładem był zrealizowany przez firmę ISCAS Sp. z o.o. projekt zrobotyzowanego stanowiska odlewniczego. Praca z topionym aluminium, rozgrzanym do 700 °C jest pełna zagrożeń i sprawia dużo trudności ludziom. Natomiast dla robota przemysłowego ciężkie warunki nie są aż tak uciążliwe. Za pomocą specjalnie zaprojektowanego narzędzia robot może nabrać odpowiednią ilość materiału i przetransportować do kokilarki – maszyny do wykonywania odlewów, gdzie aluminium jest chłodzone i po odpowiednim czasie wyjmuje się gotowy produkt. Najtrudniejszą pracę wykonuje robot, ale w tym samym momencie staje się on zagrożeniem dla pracujących wokół ludzi. Pomysłem na zachowanie bezpieczeństwa było zamknięcie robota w celi odlewniczej, z wysokimi ogrodzeniami. W ten sposób ludzie chronieni są zarówno przed robotem, jak i ewentualnymi odpryskami gorącego materiału. Tutaj pojawiły się kolejne problemy: odpowiedni dostęp produkcyjny i serwisowy. Celę wyposażono zatem w drzwi serwisowe i automatyczne drzwi otwierane po każdym zakończonym cyklu robota tak, aby pracownik mógł swobodnie wejść do maszyny i wykonać prace przygotowawcze przed kolejnym cyklem. Ponieważ urządzenia bezpieczeństwa zaczęły się mnożyć, konieczne było zintegrowanie ich w jednym systemie automatyki.
Elastyczne rozwiązanie
Sercem systemu jest sterownik Safety, do którego za pomocą magistrali PROFIsafe podłączony został sterownik WAGO z serii 750-833. Takie połączenie umożliwiało zachowanie norm przesyłu sygnałów z urządzeń bezpieczeństwa do systemu nadrzędnego, a przy jednoczesnym zastosowaniu „zwykłych” modułów konfiguracja pozwalała na przesyłanie standardowych sygnałów dwustanowych i analogowych.
Zastosowanie modułów WAGO z serii 750-66x pomogło zintegrować kilka funkcjonalności:
- Wyłączniki bezpieczeństwa
- Listwy czułe na dotyk
- Rygle bezpieczeństwa
- Czujniki kontaktronowe
- Integracja sygnałów bezpieczeństwa pochodzących z robota przemysłowego
- Wyłączanie urządzeń peryferyjnych
Ponieważ moduły WAGO spełniają wszystkie normy dotyczące architektury różnych podłączeń sygnałów bezpieczeństwa, nie było problemów z konfiguracją i parametryzacją poszczególnych kanałów. Tutaj z pomocą przyszedł WAGO-I/O-CHECK.
Konfiguracja TCI (Tool Calling Interface) / WAGO I/O moduł PROFIsafe V2
Dopełnieniem systemu automatyki było zastosowanie innych komponentów WAGO w szafie automatyki: złączki listwowe TOPJOB® S, zasilacze EPSITRON® oraz przekaźniki serii 857.
Adam Śmiałek, Kierownik Projektu ISCAS Sp. z o.o.