W drodze do Przemysłu 4.0 – system klasy MES wspiera produkcję
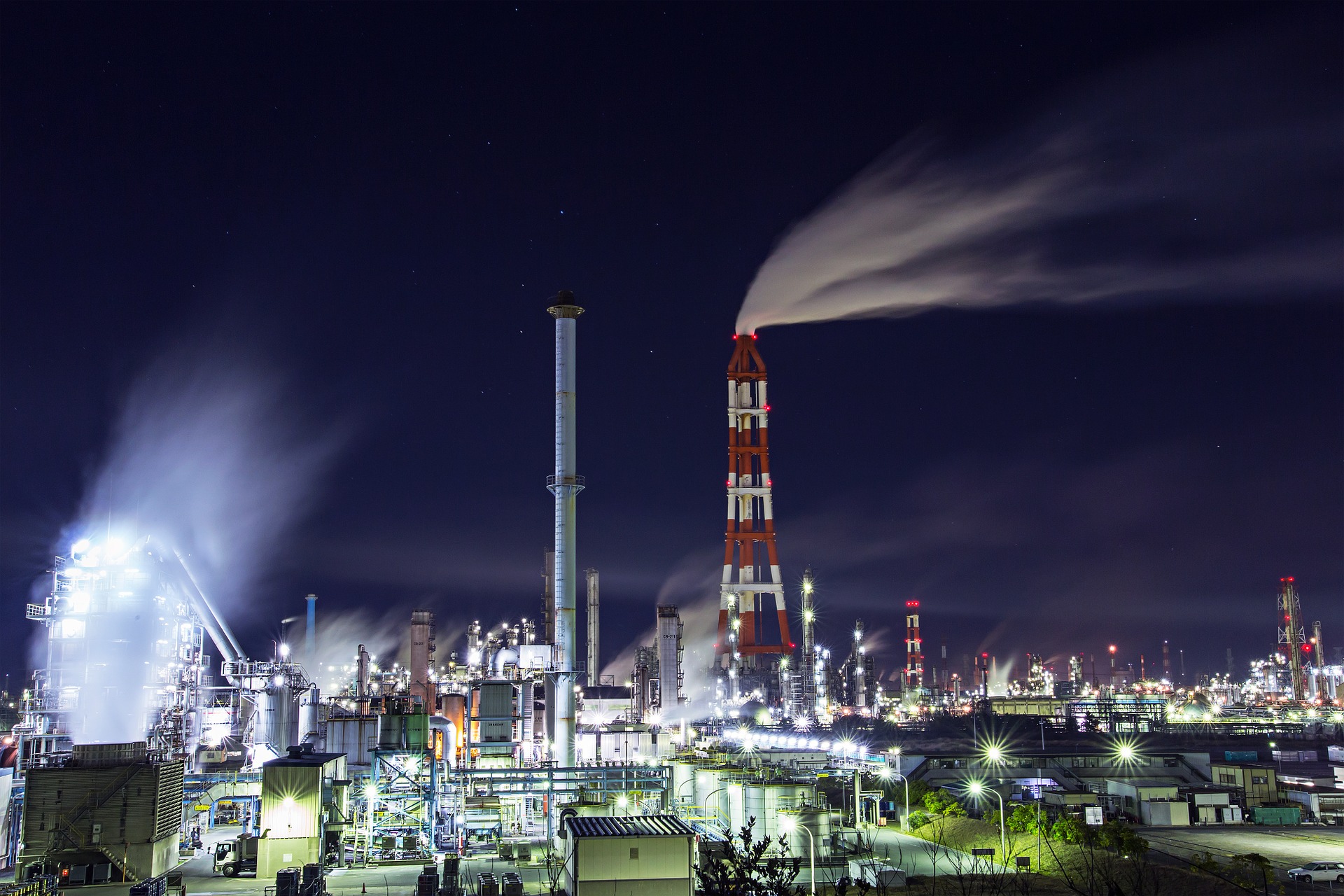
„If you can’t measure it, you can’t manage it”, mawiał Peter Drucker, amerykański autorytet w dziedzinie zarządzania.
W drodze do Przemysłu 4.0 – system klasy MES wspiera produkcję
Zagadnienia związane z zarządzaniem produkcją są dla nas istotne z co najmniej dwóch powodów. Po pierwsze: od lat w naszej ofercie znajdują się niezwykle efektywne sterowniki i moduły I/O doskonale nadające się do monitorowania stanu urządzeń. Po drugie: jesteśmy przecież wielkoseryjnym producentem komponentów wysokiej jakości.
Jeśli procesów nie można zmierzyć, to nie można nimi również zarządzać. To stwierdzenie Petera Druckera dla wielu producentów stało się punktem wyjścia do rozważań nad instalacją systemów MES. Brak przejrzystej informacji o stanie maszyn, niejasne przyczyny zakłóceń, niewystarczające dane do decyzji o koniecznych inwestycjach, ręcznie rejestrowane informacje, spóźnione raporty składające się na reaktywne, a nie zaplanowane i przejrzyste działania, były przyczyną rozpoczęcia prac nad wdrożeniem systemu MES w zakładach WAGO w 2005 roku. Od tego czasu rozwinęliśmy własny system zainstalowany w pięciu zakładach produkcyjnych, w różnych krajach, obejmujący online ponad 1000 maszyn, takich jak wtryskarki, wykrawarki, wytłaczarki, automaty montażowe, obrabiarki i drukarki przemysłowe.
Proces produkcyjny bez tajemnic
Dane zbierane są przez wystandaryzowane węzły ze sterownikami ethernetowymi 750-880, modułami I/O i specjalnie do tego przygotowanym oprogramowaniem. Każda maszyna podłączana jest poprzez specjalny kabel do dwóch modułów: dwukanałowego modułu wejść dwustanowych 750-400 i modułu licznikowego 750-404/000-005. Praktycznie każda maszyna pozwala na wyselekcjonowanie w systemie sterowania sygnałów, które po podłączeniu do wspomnianych modułów pozwalają zidentyfikować aktualny tryb pracy oraz liczbę detali (produktów) uznawanych za prawidłowe lub błędne. Dekretowania stanu maszyny dokonuje operatorka na własnym terminalu. Dzięki temu, na różnych stopniach zarządzania pracą maszyn i przebiegiem procesu, obserwujemy czasy cyklu, zakłóceń, postojów przezbrojeń. Zbieramy informacje o ilościach wyprodukowanych i brakach, obserwujemy zużycie materiałów i energii oraz przebiegi do kolejnych konserwacji.
Ponad sto węzłów dostarcza dane z ponad 1000 maszyn do naszego systemu planowania produkcji, dziennych i tygodniowych raportów. Pozwala to na świadome podejmowanie decyzji inwestycyjnych oraz optymalizację, dotyczącą modyfikacji form i narzędzi. Dzięki pracy w sieci ethernetowej sterowników WAGO integracja z istniejącą siecią biurową czy fabryczną nie stanowi problemu, a zapis danych w bazie MS-SQL Express i MySQL jest punktem wyjścia do stworzenia wygodnych wizualizacji, co sprawia, że dostęp do współczynników, takich jak stopień wykorzystania maszyn, wydajność maszyn, jakość produkcji czy OEE (overall equipment effectiveness) jest szybki i prosty.
Na własne potrzeby rozwinęliśmy swój software, pozwalający przekształcić zbierane z maszyn dane w przyjazną informację zarządczą. Jednocześnie nasze rozwiązania sprzętowe w postaci wystandaryzowanych węzłów I/O doskonale wspierają software wielu dostawców specjalizujących się w oprogramowaniu MES. Zamiast sterownika ethernetowego można zastosować sterownik do sieci Profibus, Profinet, CAN czy DeviceNet bez konieczności modyfikacji samego węzła.
Zdalna parametryzacja maszyn

Sterowniki ethernetowe wraz z modułami I/O zbierają dane i zarządzają pracą maszyn
Sterowniki ethernetowe WAGO pozwalają wejść w świat MES przy minimalnych nakładach – rolę panelu operatora może pełnić strona WWW sterownika.
W ten sam sposób można udostępniać parametry opisujące proces produkcyjny. Sam sterownik pozwala na zgromadzenie znacznej ilości danych w plikach na karcie SD, które mogą być importowane przez sieć, np. do arkuszy kalkulacyjnych. Ponieważ możliwości sterowników znacznie wykraczają poza czyste zbieranie danych, postanowiliśmy w swoich zakładach dodać możliwość zdalnej parametryzacji maszyn. Dzięki możliwościom identyfikacji operatora i ustaleniu poziomów dostępu do regulacji parametrów urządzeń jesteśmy pewni, że poszczególne nastawy wykonuje uprawniony personel. Integracja funkcji monitorowania z funkcjami parametryzowania to duży krok w kierunku automatyzacji procesów, która oznacza oszczędność czasu i zwiększenie konkurencyjności.
Michał Kownacki, WAGO.PL