Po bezpiecznej stronie, czyli jak oszacować ryzyko funkcjonowania maszyny
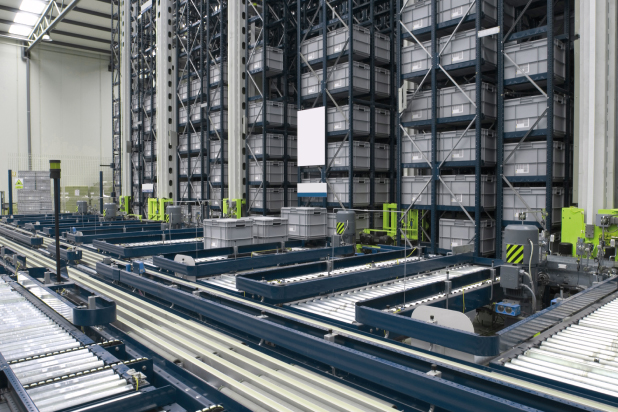
Maszyny i kompleksowe systemy stworzone dla konkretnej aplikacji powinny spełniać wszystkie założenia projektowe i wydajnościowe, ale także zapewnić bezawaryjną i bezpieczną pracę.
W Unii Europejskiej, czyli również w Polsce producentów maszyn obowiązuje Dyrektywa Maszynowa 2006/42/WE.
Poza tym mamy normy. Czym tak naprawdę one są? Czy mamy obowiązek je przestrzegać? Normy nie są aktami prawnymi, ponieważ nie są publikowane w dzienniku ustaw oraz nie są ogólnodostępne (musimy za nie zapłacić), więc nie mamy obowiązku ich przestrzegania. Czym więc są? Dla mnie są drogowskazami, które pomagają dotrzeć do celu, którym – w naszym przypadku – jest spełnienie założeń dyrektywy maszynowej, czyli wypuszczenia na rynek maszyny bezpiecznej dla użytkowników.
Norm mamy tysiące i odnoszą się tak naprawdę do wszystkiego. Jest jednak prosty sposób na dotarcie do tych, które w obecnej chwili nas interesują (np. dotyczą konkretnego typu maszyn) oraz są aktualne. Trzeba zapoznać się z normami zharmonizowanymi oraz listami norm zharmonizowanych z daną dyrektywą.
I właśnie na liście norm zharmonizowanych z dyrektywą maszynową znajduje się sławna norma ISO 13849 – Bezpieczeństwo maszyn – Elementy systemów sterowania związane z bezpieczeństwem – Część 1: Ogólne zasady projektowania, której obecne (25.08.2016) zharmonizowane wydanie ma nr PN-EN ISO 13849-1:2016-02. Wprowadza ona pojęcia kategorii bezpieczeństwa (PL), współczynniki MTTF, DC, CCF – ale o tym, kiedy indziej.
Dzisiaj skupimy się zupełnie na czym innym, na chwilę zapominamy o normie ISO 13849 i zaczynamy temat bezpieczeństwa „od początku”. Inżynieria bezpieczeństwa powinna zacząć się już na etapie projektowania układu. Niestety, bardzo często bezpieczeństwem zajmujemy się na samym końcu, co zwykle wiąże się z dodatkowymi kosztami.
Tak prawidłowo powinien wyglądać proces
A tak bardzo często wygląda
Postarajmy się ułożyć po kolei wszystkie elementy dotyczące zapewnienia bezpieczeństwa w naszej aplikacji.
Dzisiaj zajmiemy się 1 punktem, czyli oceną ryzyka. Wszystkie możliwe zagrożenia i scenariusze awarii, które mogą pojawić się w aplikacji powinny zostać przeanalizowane i poddane ocenie. Może nam w tym pomóc norma ISO 12100 (jest to również norma zharmonizowana z MD). W oparciu o otrzymane wyniki powinniśmy wyeliminować ryzyko. Jeżeli nie mryożna tego zrobić, to trzeba przynajmniej je ograniczyć. Musimy pamiętać, że analizie należy poddać wszystkie stany, w których może znaleźć się układ: tryb pracy automatycznej, tryb pracy ręcznej, konserwacji, czyszczenia itp.
Poniżej uproszczony schemat oceny ryzyka wg ISO 12100
Przeanalizujmy pierwszą część schematu, zaczynając od określenie ograniczeń maszyny i jej właściwego użytkowania.
W tym miejscu powinniśmy dokładnie określić:
– do czego maszyna jest przeznaczona,
– w jakich warunkach będzie pracowała,
– jaka jest jej wydajność.
Wszystkie założenia poczynione na tym etapie będziemy musieli zawrzeć również w instrukcji obsługi. Pozwoli to nam to ograniczyć liczbę zagrożeń, które będziemy musieli uwzględnić w kolejnych krokach. Przykład: projektujemy maszynę, która zgodnie z założeniami ma pracować w hali produkcyjnej. Dzięki wpisaniu takiego ograniczenia w analizie ryzyka możemy pominąć zagrożenia związane np. z pracą maszyny na zewnątrz (zmienne warunki atmosferyczne). Zawarcie tej informacji w instrukcji obsługi zabezpieczy nas przed ewentualnymi konsekwencjami związanymi z niewłaściwym wykorzystaniem maszyny przez użytkownika.
Identyfikacja wszystkich zagrożeń
Po określeniu ograniczeń możemy przystąpić do identyfikacji zagrożeń. I znowu pomocna może być norma ISO 12100, w której znajdują się listy kontrolne ułatwiające identyfikację zagrożeń występujących przy obsłudze maszyn i urządzeń.
Analiza ryzyka dla każdego zagrożenia
Do analizy ryzyka stosuje się najczęściej metodę wykorzystującą dwa parametry ryzyka: ciężkości następstw (skutków) występujących w aplikacji zagrożeń oraz prawdopodobieństwa, z jakim następstwa te (urazy, choroby) mogą wystąpić.
Ryzyko = rozmiar szkód x prawdopodobieństwo wystąpienia
Oszacowanie ryzyka
Po zidentyfikowaniu oraz analizie zagrożeń należy przeprowadzić oszacowanie ryzyka dla każdej rozpatrywanej sytuacji niebezpiecznej. Istnieją różne narzędzia służące do oszacowania ryzyka, np. tabele, grafy ryzyka, metody numeryczne itp.
Podczas oceny ryzyka ustalamy, czy konieczne jest zastosowanie zmian konstrukcyjnych. Jeżeli zmiany konstrukcyjne są niemożliwe, zmniejszenie poziomu ryzyka realizuje się poprzez zastosowanie technicznych środków ochronnych. Proces oceny ryzyka jest iteracją, którą kończymy po osiągnięciu akceptowalnego poziomu ryzyka i nazywamy je ryzykiem resztkowym (szczątkowym). Informacja o ryzyku resztkowym powinna znaleźć się w instrukcji obsługi.
Na koniec tej części chciałby zwrócić uwagę na jeszcze jedną sprawę. Jak można zauważyć na schemacie oceny ryzyka, mamy rozgraniczone dwa aspekty związane ze zmniejszaniem poziomu ryzyka. Są to:
– zmiany konstrukcyjne – do których możemy zaliczyć odległości bezpieczne, minimalne odstępy zapobiegające zgnieceniu ciała
– techniczne środki ochronne – do których należą osłony, kurtyny świetlne, układy sterowania.
Więcej o poziomie ryzyka w kolejnym odcinku.
Tomasz Ciesielski, WAGO.PL